What Are the Advantages to Investment Casting?
Investment casting is primarily used for metal casting projects, but there are other options. Manufacturing for metal parts can use a variety of molding methods, including aluminum die-casting, sand casting, lost wax casting, and others. While most people associate investment casting with complex shapes and dimensional precision, there are specific advantages to investment casting when compared to others.
Investment Casting vs. Other Casting Methods
Sand Casting
Investment casting uses hard ceramic molds, while sand casting uses sand mixed with clay as a bonding agent. The difference in these molds results in the finished parts; investment casting delivers smooth surfaces and low tolerances. Sand casting delivers a rough surface finish and almost always requires machining. While the molds can be changed easily in sand casting, it’s less accurate and harder to cast components with predetermined weight and size specifications.
Die Casting
In die casting, molten metal is injected into a surrounding steel cavity. Investment casting injects wax into a cavity. Because of the molten metal and high-pressure used in die casting, added machining and tooling usually drives up costs. The use of wax in investment casting allows for easier tooling and less wear on parts, keeping costs down. Also, die casting cannot be used on ferrous metals, limiting its uses.
While low-pressure die casting can deliver ideal tolerance control and surface finish, investment casting offers the most versatile method, especially for projects that require excellent precision for both ferrous and non-ferrous metals.
Lost Wax Casting
Lost wax casting refers to the original casting process of injecting wax into a permanent-molding die to form wax patterns. Since its origination (it has been around for thousands of years), advancements in casting machinery have advanced the processes to investment casting for commercial and industrial uses. The original lost-wax casting involved casting a duplicate metal sculpture from an original pattern. Today, lost wax casting is best suited to small-scale production of delicate ornaments with gold, bronze, and copper. While lost wax casting is the original process for investment casting, it’s been modernized with ceramic molds to produce metal products for transportation and engineering industries.
Overall Advantages of Investment Casting
While other casting methods may be associated with lower costs, the list of overall advantages of investment casting is long. Investment casting offers superior dimensional accuracy, a smooth surface finish, delivery on tight tolerances, and competitive pricing with lower-than-average tooling costs.
For product creators, the possibilities for production are endless, but the advantages of investment casting blends cost-efficiency with creativity and delivers industry-specific parts with complex shapes and smooth surface finishes.
Investment casting also allows for a wide range of alloys, eliminating the difficulty associated with casting challenging materials.
About KICastings
More than just an investment casting service provider, KICastings gives customers a supportive consultation process to find the right casting solutions with the best results and pricing. Rather than using third-party contractors and unreliable outsourcing, we have our own dedicated mold shop and access to the best equipment in the business. If your project requires subprocesses like finishing treatments, we can deliver a comprehensive, one-stop casting service.
Learn more about investment casting services from an expert metal casting foundry. Our services include:
- Stainless steel casting »
- Carbon steel casting »
- Copper casting »
- Alloy steel casting »
- Aluminum casting »
- Mold making »
- Precision machining »
- Low Pressure Die Casting»
- Aluminum Die Casting »
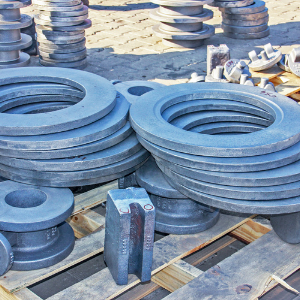
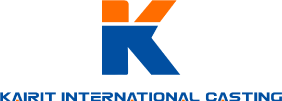